FLM230 A+B
Self-levelling screed mortars
Toepassingen
Voor het opvullen van freessleuven met vloerverwarmingsleidingen, repareren van scheuren en het uitvlakken en repareren van kleine vloeroppervlakken waarin vloerverwarming al is opgenomen. Ook geschikt voor het fixeren van elektrische vloerverwarmingsmatten. Het is een gering vloeiende mortel, samengesteld uit twee-componenten: FLM230 A + FLM230 B, die na uitharding een optisch glad resultaat geeft. Het kan direct toegepast worden als ondergrond onder harde afwerkingen zoals kurk, parket en tegelwerk.
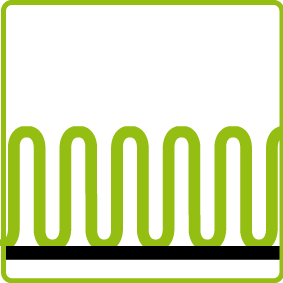
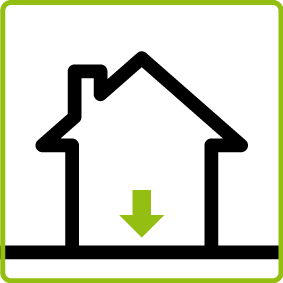
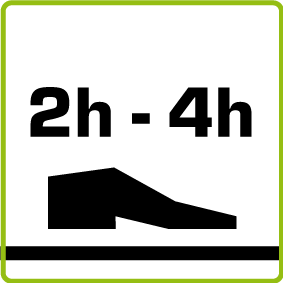
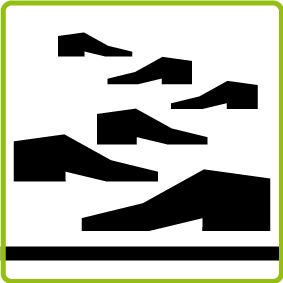
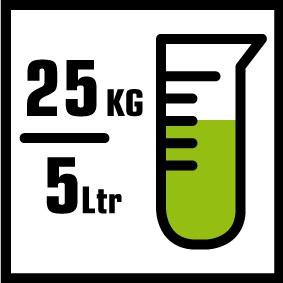
Getting started with FLM230 A+B
Certificates and documents
Download the documents available from this specific product here.
Additional documents
Can't find the right certificate?
Contact usVideos
Here you will find the videos available for this specific product. If you didn't find what you were looking for, check out our YouTube channel.
Let us help you out
The commonly used “milling of underfloor heating”, how do you finish it and why?
With milled underfloor heating it is necessary that there is good security between the existing floor and the underfloor heating pipe. Bonding/securing the pipe is a much underestimated part of the finishing process. The sand-cement floor has a somewhat hard top layer, but underneath there is a very porous layer that has a weak cohesion in practice. This may result in the following:
- The weak underlay cannot withstand the 'compressive forces' of a heating and cooling underfloor heating pipe and will come loose more than once. A repair mortar is often applied as a finishing layer. However, experience shows that this can never guarantee the adhesion necessary for sustainable and long-term use.
- This "lidding" (which lids, what is lidding?) creates hollow spaces that prevent efficient heat transfer.
- With softer floor coverings, the filling material can come loose and become compressed due to the load on tables, chairs, etc., for example. This can result in major repair costs. It is even “forbidden” to use a repair mortar for parquet.
Do the leveling compounds need to be sanded before finishing can begin?
In principle no. If, unexpectedly, small imperfections become visible the day after leveling, you can polish the floor slightly with a mesh net.
What temperature should the subfloor be during leveling?
During processing it is necessary to keep the temperature of the subfloor, space and material between 15 °C and 25 °C. In addition, the relative 65% of the lager must be before, during and a few days after maceration!